

the beginning of the process, the heater space is filled with air, which unless displaced, will reduce heat transfer and increase the warm-up time.
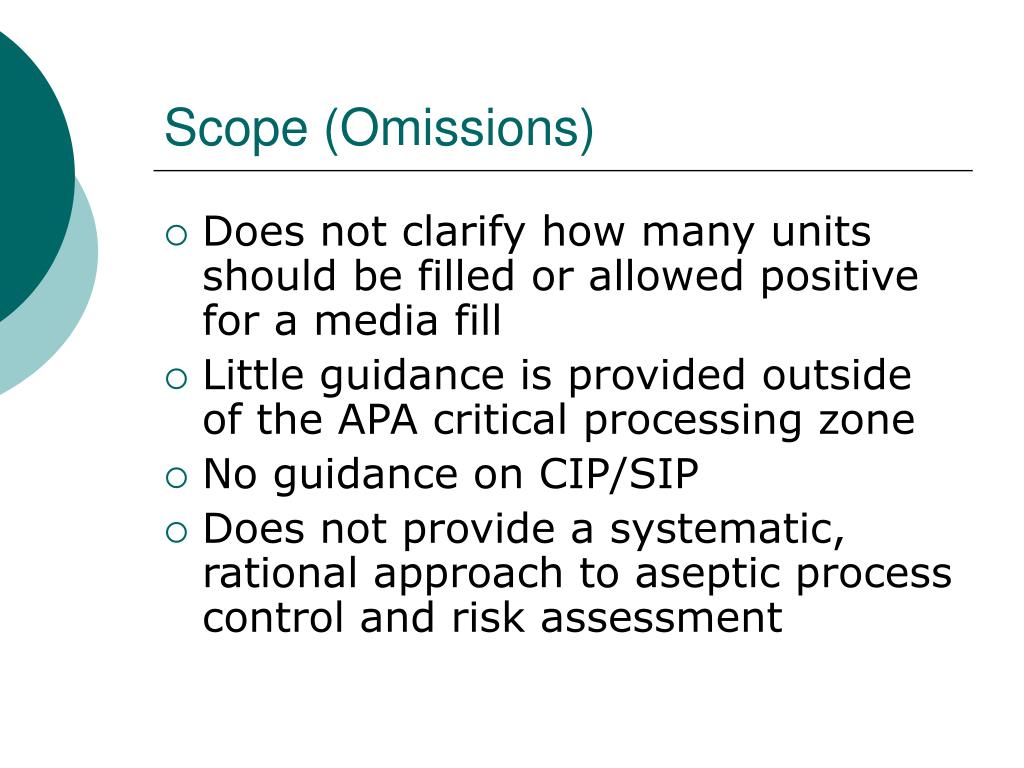
It will become clear that one type of steam trap can not possibly be the correct choice for all applications.Īt ‘start-up’, i.e. Whatever the conditions, correct steam trap selection is important to system efficiency. They may need to be resistant to corrosion or dirt. Steam traps may be subjected to extremes of temperature or even waterhammer. They may involve variations in operating pressure, heat load or condensate pressure. At first sight it may not seem obvious what these conditions are. It is imperative that the correct trap is selected to carry out a given function under given conditions. Experience shows that steam traps work most efficiently when their characteristics are matched to that of the application. To suit these varied conditions there are many different types, each having their own advantages and disadvantages. The pressures at which steam traps can operate may be anywhere from vacuum to well over a hundred bar. as soon as it forms in the steam space) or it may be required to discharge below steam temperature, giving up some of its ‘sensible heat’ in the process. It may have to discharge condensate at steam temperature (i.e. The quantity of condensate a steam trap has to deal with may vary considerably. This is the most important link in the condensate loop because it connects steam usage with condensate return.Ī steam trap quite literally ‘purges’ condensate, (as well as air and other incondensable gases), out of the system, allowing steam to reach its destination in as dry a state/condition as possible to perform its task efficiently and economically. No steam system is complete without that crucial component ‘the steam trap’ (or trap).
